Modern Foods: Disinvestment and After
|
|
ICMR HOME | Case Studies Collection
Case Details:
Case Code : BSTR018
Case Length : 14 Pages
Period : 2000-2002
Organization : MUL Modern Foods
Pub Date : 2002
Teaching Note : Available
Countries : India
Industry : Food, Beverages & Tobacco
To download Modern Foods: Disinvestment and After case study (Case Code: BSTR018) click on the button below, and select the case from the list of available cases:
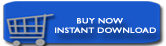
OR

Buy With PayPal
|
Price:
For delivery in electronic format: Rs. 300 ; For delivery through courier (within India): Rs. 300 + Shipping & Handling Charges extra
»
Business Strategy Case Studies
» Business Strategy Short Case Studies
» View Detailed Pricing Info
» How To Order This Case » Business Case Studies » Area Specific Case Studies
» Industry Wise Case Studies
» Company Wise Case Studies
Please note:
This case study was compiled from published sources, and is intended to be used as a basis for class discussion. It is not intended to illustrate either effective or ineffective handling of a management situation. Nor is it a primary information source.
Chat with us

Please leave your feedback
|

<< Previous
Background Note
Modern Bakeries (India) Limited, incorporated in October 1965, was renamed Modern Food Industries (India) Limited (MFIL) on 11th November 1982. The company had 14 bakery units located in 13 cities and 6 other units at other places.
Its products were bread, oil, flour, fruit pulp, fruit juice drinks, beverage concentrates and energy food. In the early 1990s, the bakery units accounted for 82% of the turnover of MFIL. In the early 1990s, due to labour trouble, decline in market demand and the closure of a plant, capacity utilisation remained low, between 19% and 30% at the Ranchi unit, between 31% and 53% in the Calcutta unit, and below 50% in the Jaipur, Kanpur and Delhi-11 units. (Refer Exhibit III for unit-wise capacity, production and profits). Consequently, many bakery units were running at a loss. MFIL fixed a norm of 0.50% of total production as defective production. In addition, a norm of 0.50% for bread returned from the market was also allowed.
|
|
However, the percentage of defective production and return of unsold, damaged and defective bread exceeded the norms (Refer Exhibit IV & V).
|
Upto 1993-94, the cumulative losses of MFIL's Roller Flour Mill, Fruit Juice Bottling I Plant, Fruit Pulp Processing Plant and Oil Plant were Rs 11.85 million, Rs.64.4 million, Rs.32.40 million and Rs.81.94 million respectively. In 1997, MFIL was referred to the Disinvestment Commission.4 In February 1997, the Commission recommended 100% sale of the company. While making this recommendation, the Disinvestment Commission identified some of MFIL's weaknesses: under- utilisation
of the production facilities, large work force, low productivity and
limited flexibility in decision-making. In September 1997, the
government approved 50% disinvestment to a strategic partner through
competitive global bidding... |
Excerpts >>
|
|